In today’s fast-paced business landscape, efficient warehouse operations are crucial for maintaining a competitive edge. As customer expectations rise and supply chains become increasingly complex, the need for a robust Warehouse Management System (WMS) has never been greater. However, many businesses still rely on outdated or manual processes, failing to recognize the hidden costs associated with neglecting investments in modern warehouse management software.
A WMS is a powerful tool that streamlines and optimizes various aspects of warehouse operations, from inventory management and order fulfillment to labor productivity and space utilization. By ignoring the benefits of a WMS, businesses inadvertently incur significant costs that can hinder their growth and profitability. In this blog post, we’ll explore the hidden costs of neglecting warehouse management software investments and the potential impact on your bottom line.
- Inefficient Inventory Management One of the primary functions of a WMS is to provide real-time visibility and tracking of inventory levels across multiple warehouses or distribution centers. Without a comprehensive WMS, businesses often struggle with inaccurate inventory records, stockouts, and excess inventory, leading to lost sales opportunities, increased carrying costs, and potential obsolescence.
Manual inventory management processes are not only time-consuming but also prone to human error, resulting in costly discrepancies between physical stock and recorded quantities. A WMS eliminates these issues by automating inventory tracking, enabling cycle counting, and integrating barcode or RFID scanning for real-time data capture.
- Suboptimal Order Fulfillment and Shipping Processes In today’s e-commerce era, customers expect fast and accurate order fulfillment. Neglecting investments in a WMS can severely impact your ability to meet these expectations, leading to dissatisfied customers, increased returns, and potential loss of business.
Without a WMS, picking and packing processes are often manual and inefficient, resulting in longer order processing times, higher labor costs, and increased errors. A WMS optimizes these processes by providing features such as wave planning, pick path optimization, and real-time order tracking, ensuring orders are fulfilled accurately and efficiently.
Furthermore, a WMS streamlines shipping and receiving processes by automating tasks like carrier selection, label printing, and shipment tracking, reducing the risk of delays and ensuring timely deliveries.
- Diminished Labor Productivity Warehouse operations are inherently labor-intensive, and inefficient processes can significantly impact workforce productivity. Without a WMS, tasks such as picking, putaway, and replenishment are often performed manually, leading to wasted time, increased fatigue, and higher error rates.
A WMS provides tools for optimizing labor utilization, such as task interleaving, zone picking, and directed workflows. By automating and streamlining these processes, a WMS minimizes non-value-added activities, improves employee productivity, and reduces the risk of costly errors.
- Poor Space Utilization and Asset Tracking Effective space utilization is critical in warehouse operations, as it directly impacts operating costs and capacity. Neglecting investments in a WMS can result in inefficient use of available space, leading to higher real estate costs, increased handling times, and potential safety hazards.
A WMS incorporates advanced slotting and putaway logic, ensuring optimal placement of inventory based on factors such as product characteristics, demand patterns, and ergonomics. This not only maximizes space utilization but also improves picking efficiency and reduces travel time within the warehouse.
Additionally, a WMS provides robust asset tracking capabilities, enabling businesses to monitor and manage the utilization of valuable assets like forklifts, pallets, and racking systems, reducing the risk of loss or misplacement.
- Inadequate Returns and Reverse Logistics Management In today’s competitive market, efficient returns and reverse logistics processes are essential for delivering exceptional customer service and minimizing the financial impact of product returns. Without a WMS, managing these processes can be challenging and costly.
A WMS streamlines reverse logistics by automating tasks such as returns processing, product inspection, and disposition decision-making. It also provides visibility into returned inventory, enabling businesses to quickly identify root causes and implement corrective actions, reducing the risk of future returns and associated costs.
- Lack of Compliance and Regulatory Adherence Warehouses and distribution centers are subject to various compliance and regulatory requirements, ranging from product traceability and safety standards to environmental and labor regulations. Failing to adhere to these regulations can result in hefty fines, legal liabilities, and damage to your brand reputation.
A WMS plays a crucial role in ensuring compliance by providing features such as lot and serial number tracking, expiration date management, and electronic record-keeping. By automating these processes, a WMS minimizes the risk of non-compliance and helps businesses maintain a strong track record of regulatory adherence.
- Increased Operational Costs The hidden costs of neglecting warehouse management software investments often manifest in the form of increased operational costs. Manual processes, inefficient workflows, and lack of visibility can lead to higher labor expenses, excessive inventory carrying costs, and increased transportation and logistics costs.
A WMS helps businesses minimize these operational costs by optimizing processes, reducing errors and inefficiencies, and providing real-time visibility into inventory levels and resource utilization. Additionally, a WMS can integrate with other supply chain systems, such as transportation management systems (TMS) and enterprise resource planning (ERP) solutions, further streamlining operations and reducing costs.
- Missed Opportunities for Warehouse Automation As technology continues to advance, warehouse automation has become increasingly accessible and beneficial for businesses of all sizes. However, without a robust WMS, the potential benefits of automation may be limited or even negated entirely.
A WMS serves as the backbone for warehouse automation, enabling seamless integration with automated systems such as conveyor systems, automated storage and retrieval systems (AS/RS), and robotic picking solutions. By neglecting investments in a WMS, businesses may miss out on opportunities to enhance efficiency, reduce labor costs, and improve overall operational performance through automation.
- Limited Scalability and Growth Potential As your business grows and expands, so too will the complexity of your warehouse operations. Without a flexible and scalable WMS, managing this growth can become increasingly challenging, hindering your ability to capitalize on new opportunities and meet increasing customer demands.
A WMS is designed to scale seamlessly, accommodating additional warehouses, product lines, and operational complexity. By neglecting investments in a WMS, businesses may find themselves constrained by manual processes and legacy systems, ultimately limiting their growth potential and competitiveness in the market.
Conclusion Investing in a robust Warehouse Management System (WMS) is no longer an option but a necessity for businesses seeking to optimize their warehouse operations and maintain a competitive edge. The hidden costs of neglecting these investments can be substantial, impacting everything from inventory accuracy and order fulfillment efficiency to labor productivity and regulatory compliance.
By embracing a WMS, businesses can unlock a wealth of benefits, including streamlined processes, improved visibility, enhanced customer satisfaction, and ultimately, reduced operational costs. As the demands of modern supply chains continue to evolve, a WMS will become an indispensable tool for businesses striving to remain agile, efficient, and profitable.
Don’t let the hidden costs of neglecting warehouse management software investments hold your business back. Embrace the power of a WMS and position your organization for sustained growth and success in an increasingly competitive marketplace.
Get in Touch
We know what NetSuite can do and how it can help you. Schedule your free NetSuite assessment today
FAQs:
A Warehouse Management System (WMS) is a software solution that optimizes and manages various aspects of warehouse operations, such as inventory management, order fulfillment, labor productivity, and space utilization.
A WMS is crucial because it streamlines and automates warehouse processes, reducing errors, increasing efficiency, and providing real-time visibility into operations, which helps businesses meet rising customer expectations and manage complex supply chains effectively.
Without a WMS, businesses face inefficient inventory management, suboptimal order fulfillment, diminished labor productivity, poor space utilization, inadequate returns management, compliance issues, increased operational costs, missed automation opportunities, and limited scalability.
A WMS improves inventory management by providing real-time tracking and visibility of inventory levels, automating inventory tracking, enabling cycle counting, and integrating barcode or RFID scanning to reduce discrepancies and stockouts.
A WMS optimizes order fulfillment and shipping by automating picking and packing processes, offering features like wave planning and pick path optimization, and streamlining shipping tasks such as carrier selection and label printing to ensure accurate and timely deliveries.
A WMS enhances labor productivity by automating manual tasks, reducing non-value-added activities, and providing tools for task interleaving, zone picking, and directed workflows, which minimizes errors and improves overall efficiency.
A WMS optimizes space utilization by using advanced slotting and putaway logic, ensuring efficient placement of inventory. It also provides robust asset tracking capabilities to monitor and manage the use of valuable assets like forklifts and pallets.
A WMS is critical for managing returns and reverse logistics because it automates returns processing, product inspection, and disposition decision-making, providing visibility into returned inventory and helping to identify and address root causes of returns efficiently.
A WMS ensures compliance by automating processes such as lot and serial number tracking, expiration date management, and electronic record-keeping, which helps businesses adhere to various regulatory requirements and avoid legal and financial penalties.
The long-term benefits of investing in a WMS include reduced operational costs, improved efficiency, enhanced customer satisfaction, better inventory and order management, seamless integration with other supply chain systems, and scalable solutions that support business growth and adaptability.
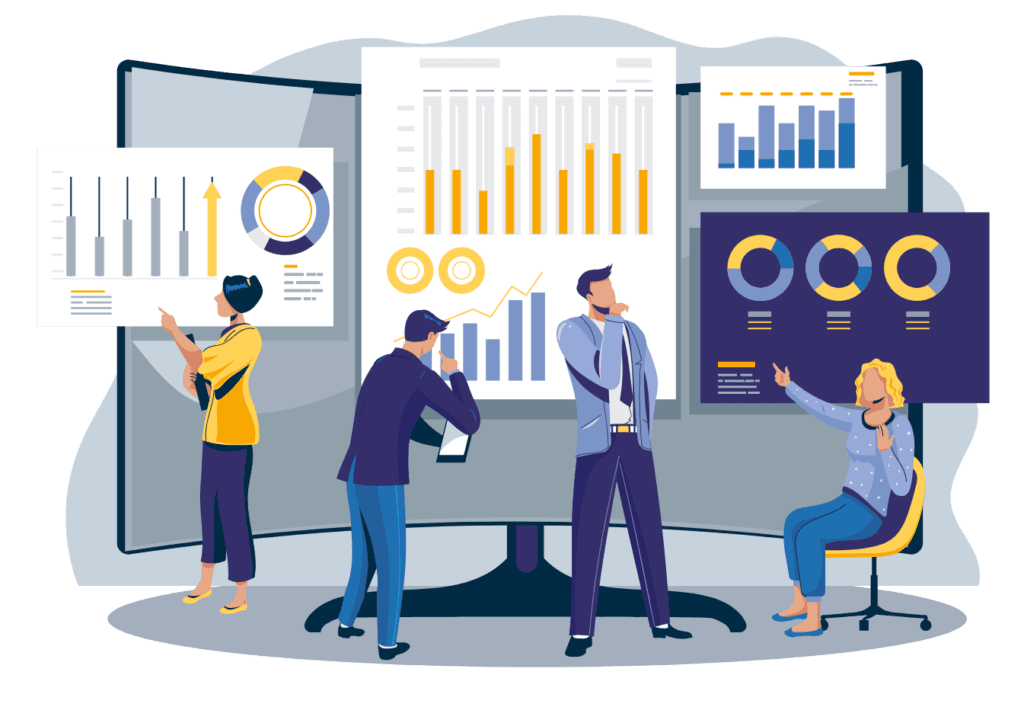