Unlocking the Power of NetSuite for Predictive Maintenance in Manufacturing
The manufacturing industry is undergoing a digital transformation, and at the forefront of this shift is the integration of advanced technologies like predictive maintenance. As manufacturers strive to optimize operations, reduce downtime, and improve asset performance, NetSuite emerges as a powerful tool to support these initiatives. In this blog post, we’ll explore how NetSuite’s robust features and capabilities can revolutionize predictive maintenance strategies in manufacturing, unlocking new levels of efficiency and productivity.
Understanding Predictive Maintenance in Manufacturing
Before diving into the specifics of NetSuite’s role in predictive maintenance, let’s first understand what predictive maintenance entails. Predictive maintenance is a proactive approach that leverages data, analytics, and advanced algorithms to anticipate equipment failures before they occur. By monitoring key performance indicators and analyzing historical data, predictive maintenance enables manufacturers to schedule maintenance tasks at optimal times, minimizing disruptions to production and maximizing asset reliability.
The importance of predictive maintenance in manufacturing cannot be overstated. Unplanned downtime due to equipment failures can lead to significant financial losses, decreased productivity, and customer dissatisfaction. By implementing predictive maintenance strategies, manufacturers can:
– Reduce unplanned downtime and associated costs
– Extend the lifespan of critical assets
– Optimize maintenance schedules and resource allocation
– Improve overall equipment effectiveness (OEE)
– Enhance safety by preventing catastrophic failures
The benefits of predictive maintenance extend beyond just reducing downtime. By proactively addressing potential issues, manufacturers can also:
– Minimize spare parts inventory costs by ordering parts just-in-time
– Reduce energy consumption by operating equipment at optimal conditions
– Improve product quality by ensuring equipment is running at peak performance
– Enhance customer satisfaction by meeting delivery commitments consistently
Predictive maintenance is a key enabler of smart manufacturing, allowing organizations to leverage data and technology to drive operational excellence. As Industry 4.0 continues to shape the future of manufacturing, predictive maintenance will play an increasingly crucial role in staying competitive.
NetSuite: The Ideal Platform for Predictive Maintenance
NetSuite, a leading cloud-based enterprise resource planning (ERP) solution, offers a comprehensive suite of features that perfectly align with the needs of predictive maintenance in manufacturing. With its robust manufacturing industry solutions, NetSuite provides the foundation for implementing effective predictive maintenance strategies.
- Data Collection and Integration
At the core of predictive maintenance lies data. NetSuite’s IoT integration capabilities allow manufacturers to seamlessly connect and collect data from various sources, including sensors, machines, and other smart devices. This data forms the basis for predictive analytics, enabling real-time monitoring and analysis of equipment performance.
NetSuite’s integration with IoT platforms and industrial control systems ensures that data is collected accurately and efficiently. Manufacturers can define data collection intervals, set up automated data transfer processes, and ensure data integrity through validation rules. This seamless integration eliminates manual data entry errors and provides a reliable foundation for predictive maintenance analytics.
- Advanced Analytics and Reporting
NetSuite’s built-in analytics and reporting tools empower manufacturers to gain valuable insights from the collected data. With NetSuite’s predictive analytics capabilities, manufacturers can identify patterns, trends, and anomalies that indicate potential equipment issues. Customizable dashboards and reports provide a clear overview of key performance metrics, allowing teams to make data-driven decisions and take proactive measures.
NetSuite’s analytics tools leverage advanced algorithms and machine learning techniques to analyze historical data and predict future equipment behavior. Manufacturers can set up alerts and notifications based on predefined thresholds, ensuring that maintenance teams are promptly notified of potential issues. These insights enable manufacturers to prioritize maintenance tasks, allocate resources effectively, and minimize the risk of unexpected failures.
- Asset Management and Maintenance Scheduling
NetSuite’s asset management features streamline the tracking and management of manufacturing assets. Manufacturers can maintain detailed records of equipment, including maintenance history, spare parts inventory, and warranty information. This centralized asset database facilitates efficient maintenance planning and scheduling.
NetSuite allows manufacturers to set up preventive maintenance schedules based on predefined criteria, such as usage hours or production cycles. With predictive maintenance insights, these schedules can be further optimized to align with the actual condition of the equipment, ensuring maintenance tasks are performed at the most opportune times.
Manufacturers can also track asset performance metrics, such as uptime, downtime, and mean time between failures (MTBF). These metrics provide valuable insights into asset reliability and help identify areas for improvement. NetSuite’s asset management capabilities enable manufacturers to make informed decisions about asset replacement, upgrades, and capacity planning.
- Work Order Management and Collaboration
When predictive maintenance identifies a potential issue, NetSuite’s work order management capabilities spring into action. Manufacturers can easily create, assign, and track maintenance work orders, ensuring that the right technicians are dispatched with the necessary tools and parts. NetSuite’s collaborative features facilitate communication between maintenance teams, production staff, and other stakeholders, streamlining the maintenance process and minimizing downtime.
NetSuite’s work order management system allows manufacturers to define maintenance workflows, set priorities, and track progress in real-time. Technicians can access detailed work instructions, safety procedures, and equipment manuals directly from the work order, ensuring accurate and efficient maintenance execution. Collaboration tools, such as chat and file sharing, enable seamless communication and knowledge sharing among team members.
- Mobile Accessibility and Real-Time Updates
NetSuite’s cloud-based architecture and mobile-friendly interface enable manufacturers to access critical maintenance information anytime, anywhere. Maintenance technicians can use mobile devices to view work orders, update status, and capture important data points directly from the field. This real-time accessibility ensures that everyone stays informed and can make prompt decisions based on the most up-to-date information.
Mobile accessibility also enhances the efficiency of maintenance operations. Technicians can easily access equipment history, spare parts information, and technical documentation while on the go. They can capture photos, videos, and voice notes to document maintenance activities and share them with the team in real-time. This mobile connectivity streamlines communication, reduces paperwork, and improves the overall effectiveness of maintenance processes.
- Integration with Industry 4.0 Technologies
NetSuite’s flexibility and open architecture allow seamless integration with other Industry 4.0 technologies, such as IoT devices, machine learning algorithms, and automation systems. This integration enables manufacturers to create a connected ecosystem where data flows seamlessly between systems, enhancing the accuracy and effectiveness of predictive maintenance strategies.
For example, data from IoT sensors can be automatically fed into NetSuite, triggering predictive maintenance workflows based on predefined thresholds. Machine learning algorithms can continuously analyze this data, refining predictive models and improving the accuracy of failure predictions over time.
Integration with automation systems allows manufacturers to automate maintenance tasks, such as scheduling work orders, ordering spare parts, and updating asset records. This automation reduces manual intervention, minimizes human errors, and improves the efficiency of maintenance operations. NetSuite’s integration capabilities ensure that predictive maintenance is seamlessly woven into the overall manufacturing ecosystem.
- Scalability and Customization
One of the key advantages of NetSuite is its scalability. As manufacturing operations grow and evolve, NetSuite can easily adapt to accommodate new assets, production lines, and maintenance requirements. The platform’s customization capabilities allow manufacturers to tailor predictive maintenance workflows and reports to their specific needs, ensuring a perfect fit for their unique processes.
NetSuite’s scalability enables manufacturers to start small and gradually expand their predictive maintenance initiatives. They can begin by implementing predictive maintenance for critical assets and then scale up to include additional equipment and production lines. NetSuite’s flexible architecture ensures that the system can handle increasing data volumes and complexity as the predictive maintenance program expands.
Customization is another powerful aspect of NetSuite. Manufacturers can configure data fields, workflows, and reports to align with their specific industry requirements and business processes. They can create custom dashboards and key performance indicators (KPIs) to track the metrics that matter most to their organization. This customization ensures that NetSuite delivers maximum value and supports the unique needs of each manufacturer.
Real-World Success Stories
Numerous manufacturers across various industries have already embraced NetSuite for predictive maintenance, achieving remarkable results. Let’s take a look at a few real-world success stories:
- Aerospace Manufacturer
An aerospace manufacturer implemented NetSuite to monitor the health of its critical production equipment. By leveraging predictive maintenance, they were able to reduce unplanned downtime by 30%, improve overall equipment effectiveness by 15%, and extend the lifespan of their assets. NetSuite’s real-time insights and automated maintenance workflows played a crucial role in achieving these outcomes.
The manufacturer integrated NetSuite with their IoT sensors and SCADA systems, enabling real-time data collection and analysis. predictive maintenance algorithms identified potential issues in advance, allowing the maintenance team to schedule proactive interventions during planned downtime. This approach minimized production disruptions and ensured a consistent supply of high-quality components to their customers.
- Food and Beverage Producer
A leading food and beverage producer integrated NetSuite with their production lines to optimize maintenance schedules. Through predictive analytics, they identified potential failures in their packaging equipment, enabling proactive maintenance interventions. As a result, they reduced downtime by 25%, increased production efficiency, and improved product quality consistency.
NetSuite’s asset management features allowed the producer to track the performance and maintenance history of each packaging machine. This data-driven approach helped them identify patterns and trends, leading to more accurate failure predictions. The maintenance team received automated alerts when equipment performance deviated from normal ranges, enabling them to take timely action and prevent unplanned stoppages.
- Automotive Parts Manufacturer
An automotive parts manufacturer leveraged NetSuite’s IoT integration to collect real-time data from their machinery. By analyzing this data using NetSuite’s predictive analytics tools, they were able to detect anomalies and predict impending failures. This proactive approach allowed them to schedule maintenance during planned downtime, minimizing disruptions to production schedules and reducing maintenance costs by 20%.
The manufacturer also utilized NetSuite’s work order management system to streamline maintenance workflows. Technicians received detailed work instructions and had access to equipment manuals and spare parts information directly from their mobile devices. This connectivity improved the efficiency and effectiveness of maintenance operations, ensuring that the manufacturer could meet the stringent quality and delivery requirements of the automotive industry.
These success stories demonstrate the tangible benefits that manufacturers can achieve by embracing NetSuite for predictive maintenance. By unlocking the power of data, analytics, and automation, NetSuite empowers manufacturers to optimize their maintenance strategies, improve operational efficiency, and gain a competitive edge in the market.
Implementing NetSuite for Predictive Maintenance
If you’re a manufacturer looking to harness the power of predictive maintenance, implementing NetSuite is a strategic move. Here’s a step-by-step guide to getting started:
- Assess Your Current Maintenance Practices
Before implementing NetSuite, evaluate your current maintenance practices and identify areas for improvement. Determine which assets are critical to your operations and would benefit most from predictive maintenance. Consider factors such as asset age, maintenance history, and downtime impact.
Conduct a thorough assessment of your existing maintenance processes, data collection methods, and technology infrastructure. Identify any gaps or limitations that need to be addressed to enable effective predictive maintenance. This assessment will provide a solid foundation for planning your NetSuite implementation.
- Define Your Predictive Maintenance Goals
Clearly define your predictive maintenance goals and objectives. What specific outcomes do you want to achieve? This could include reducing downtime, extending asset lifespan, improving maintenance efficiency, or enhancing product quality. Having well-defined goals will guide your implementation strategy and help measure success.
Engage stakeholders from various departments, including maintenance, production, quality, and finance, to gather their input and align goals across the organization. Establish key performance indicators (KPIs) and targets to track progress towards your predictive maintenance objectives. These KPIs could include metrics such as overall equipment effectiveness (OEE), mean time between failures (MTBF), and maintenance cost savings.
- Engage With a NetSuite Partner
Partnering with an experienced NetSuite implementation partner can greatly streamline the process. Look for a partner with expertise in manufacturing and predictive maintenance. They can provide valuable guidance, best practices, and customization support to ensure a smooth and successful implementation.
Your NetSuite partner will work closely with your team to understand your unique requirements, design the optimal system architecture, and configure NetSuite to meet your specific needs. They can also provide training and support to ensure your team is fully equipped to leverage the power of NetSuite for predictive maintenance.
- Integrate Data Sources
Identify the data sources that will feed into your predictive maintenance system. This may include IoT sensors, SCADA systems, production equipment, and maintenance records. Work with your NetSuite partner to establish data integration pipelines and ensure seamless data flow into the NetSuite platform.
Define data standards and protocols to ensure data consistency and integrity across different sources. Establish automated data collection processes to minimize manual intervention and ensure timely data availability for predictive analytics. Test and validate data integration to ensure accurate and reliable data flow into NetSuite.
- Configure Predictive Maintenance Workflows
Configure NetSuite to support your predictive maintenance workflows. This involves setting up asset records, defining maintenance schedules, configuring predictive analytics rules, and establishing work order management processes. Your NetSuite partner can assist in tailoring these configurations to align with your specific requirements.
Define the criteria and thresholds for triggering predictive maintenance alerts and work orders. Configure automated workflows to streamline maintenance processes, such as generating work orders, assigning tasks to technicians, and updating asset records. Establish approval workflows and notification mechanisms to ensure proper oversight and communication throughout the maintenance lifecycle.
- Train Your Team
Provide comprehensive training to your maintenance team, production staff, and other relevant stakeholders on how to use NetSuite for predictive maintenance. Ensure they understand how to interpret dashboards, generate reports, create work orders, and update maintenance records. Proper training is essential for successful adoption and effective utilization of the system.
Develop training materials and user guides tailored to your specific NetSuite configuration and workflows. Conduct hands-on training sessions to familiarize users with the system and its features. Provide ongoing support and refresher training to ensure users remain proficient and can fully leverage the capabilities of NetSuite for predictive maintenance.
- Monitor, Analyze, and Continuously Improve
Once NetSuite is implemented, continuously monitor the performance of your predictive maintenance program. Regularly analyze the data, track key performance indicators, and identify areas for improvement. Use the insights gained to refine your predictive models, optimize maintenance schedules, and drive continuous improvement initiatives.
Establish regular review meetings to discuss the effectiveness of your predictive maintenance strategies. Engage cross-functional teams to share insights, best practices, and lessons learned. Continuously refine your predictive maintenance workflows based on feedback from maintenance technicians, production staff, and other stakeholders.
Leverage NetSuite’s reporting and analytics capabilities to generate actionable insights and support data-driven decision-making. Monitor trends, identify patterns, and proactively address any issues or opportunities for improvement. Continuously iterate and enhance your predictive maintenance program to drive ongoing operational excellence.
The Future of Manufacturing with Predictive Maintenance
As the manufacturing industry continues to evolve, predictive maintenance will play an increasingly crucial role in driving operational excellence. NetSuite, with its robust features and scalability, is well-positioned to support manufacturers in their predictive maintenance journey.
Looking ahead, we can expect further advancements in IoT technologies, machine learning algorithms, and data analytics capabilities. These advancements will enhance the accuracy and effectiveness of predictive maintenance strategies, enabling manufacturers to achieve even greater levels of efficiency and productivity.
Moreover, the integration of predictive maintenance with other Industry 4.0 technologies, such as artificial intelligence, augmented reality, and digital twins, will open up new possibilities for manufacturers. For example, augmented reality can be used to guide maintenance technicians through complex repairs, while digital twins can simulate equipment behavior and predict failures with even greater precision.
NetSuite, with its flexible and adaptable architecture, is ready to accommodate these future advancements. As new technologies emerge, NetSuite will continue to evolve and integrate with them seamlessly, ensuring that manufacturers can stay at the forefront of predictive maintenance innovation.
The future of manufacturing lies in the ability to harness the power of data and technology to drive operational excellence. Predictive maintenance, powered by NetSuite, will be a key enabler of this transformation. Manufacturers who embrace this shift and leverage the capabilities of NetSuite will be well-positioned to thrive in the Industry 4.0 era.
Conclusion
Predictive maintenance is a game-changer for the manufacturing industry, offering unparalleled opportunities for optimization, efficiency, and growth. By unlocking the power of NetSuite for predictive maintenance, manufacturers can harness the full potential of their assets, reduce downtime, and drive operational excellence.
As a comprehensive cloud-based ERP solution, NetSuite provides the tools and capabilities necessary to implement effective predictive maintenance strategies. From data collection and integration to advanced analytics and maintenance workflow management, NetSuite empowers manufacturers to proactively manage their assets and make data-driven decisions.
Real-world success stories demonstrate the tangible benefits that manufacturers can achieve by embracing NetSuite for predictive maintenance. Reduced downtime, improved asset performance, and increased operational efficiency are just a few of the outcomes that manufacturers have realized.
As the manufacturing industry continues to evolve, predictive maintenance will become increasingly crucial for staying competitive. NetSuite, with its scalability, flexibility, and continuous innovation, is the ideal platform for manufacturers looking to unlock the full potential of predictive maintenance.
If you’re ready to transform your manufacturing operations with predictive maintenance, NetSuite is the key to success. Partner with an experienced NetSuite implementation partner, define your goals, and embark on a journey towards a smarter, more efficient, and more profitable future.
Remember, the power of predictive maintenance lies in your hands. Unlock it with NetSuite and revolutionize your manufacturing operations today. Embrace the future of manufacturing and position your organization for success in the Industry 4.0 era.
Get in Touch
We know what NetSuite can do and how it can help you. Schedule your free NetSuite assessment today
FAQs:
Predictive maintenance is a proactive approach where data, analytics, and advanced algorithms are used to predict potential equipment failures before they happen. By monitoring equipment performance and analyzing historical data, manufacturers can schedule maintenance at optimal times, reducing disruptions and extending asset lifespan.
Predictive maintenance helps manufacturers by reducing unplanned downtime, improving asset reliability, optimizing maintenance schedules, enhancing safety, and minimizing costs. It also helps extend the life of critical assets, improve product quality, and maintain customer satisfaction by ensuring timely deliveries.
NetSuite offers comprehensive features, such as IoT integration, advanced analytics, asset management, and work order management, that align well with predictive maintenance needs. Its cloud-based architecture allows real-time monitoring, while its scalable and customizable capabilities support manufacturers as they grow and refine their maintenance processes.
NetSuite integrates with IoT platforms and industrial control systems, allowing seamless data collection from sensors and machines. This data provides the foundation for predictive maintenance analytics, enabling real-time monitoring and the early detection of potential equipment issues.
Yes, NetSuite can optimize maintenance schedules by combining predefined preventive maintenance schedules with predictive insights. This ensures maintenance is performed when needed, based on actual equipment condition, which helps reduce downtime and improve operational efficiency.
NetSuite streamlines work order management by allowing manufacturers to create, assign, and track maintenance tasks. It ensures technicians receive accurate work instructions and relevant equipment data. Real-time updates and collaboration features improve communication between maintenance teams and production staff, minimizing downtime.
Yes, NetSuite offers mobile accessibility, allowing maintenance technicians to access critical information, work orders, and updates from anywhere. Mobile devices enable them to capture data, view equipment history, and communicate with the team in real-time, enhancing maintenance efficiency.
NetSuite’s open architecture allows it to integrate with other Industry 4.0 technologies, such as IoT devices, machine learning, and automation systems. This enables manufacturers to create a connected ecosystem where data flows seamlessly between systems, enhancing predictive maintenance efforts and improving accuracy.
Yes, NetSuite is highly scalable. As manufacturing operations expand, the platform can easily accommodate additional assets, production lines, and maintenance requirements. Its customization options also allow businesses to tailor workflows and reports to their specific needs.
To implement NetSuite for predictive maintenance, manufacturers should first assess current maintenance practices, define goals, and engage a NetSuite partner. The next steps include integrating data sources, configuring predictive maintenance workflows, training teams, and continuously monitoring performance to refine processes and improve results.
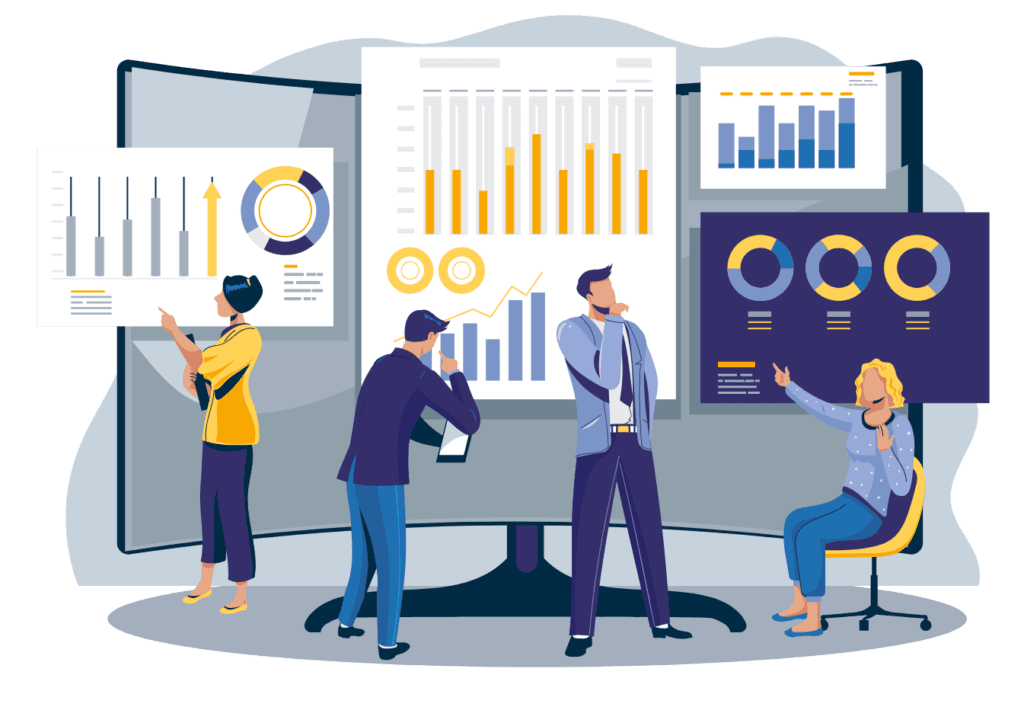