Advanced Lot Tracking Strategies in NetSuite
For businesses that deal with perishable goods, regulated products, or items that require detailed traceability, having a robust lot tracking system is essential. Lot tracking allows you to monitor inventory at a granular level, tracing specific batches of product from suppliers through production and all the way to end customers.
NetSuite offers powerful native tools for implementing advanced lot tracking strategies. By leveraging NetSuite’s lot tracking capabilities, you can achieve complete visibility into your inventory, enhance quality control, streamline compliance processes, and enable targeted recalls if needed. Let’s explore some key strategies and best practices for advanced lot tracking in NetSuite.
Defining Your Lot Numbering Scheme
The foundation of effective lot tracking is a well-designed lot numbering system. In NetSuite, you have the flexibility to define lot numbers according to your business requirements. Consider factors like product type, expiration dates, manufacturing facility, and supplier when devising your lot numbering scheme.
For example, a food manufacturer might use a lot number that includes the production date, product code, and batch number, such as 20230530-APP-001 for a batch of applesauce produced on May 30, 2023. A pharmaceutical company could incorporate the drug name, strength, expiration date, and a serial number, like DRUXA100-20241231-00001.
The key is to establish a consistent, meaningful format that allows you to quickly identify and sort lots based on relevant criteria. NetSuite supports both numeric and alphanumeric lot numbers up to 30 characters in length, giving you ample room to encode important information.
When designing your lot numbering scheme, it’s also important to consider any industry-specific requirements or standards. For example, the GS1 Global Trade Item Number (GTIN) standard is widely used in the retail and healthcare sectors. If your business operates in a regulated industry, ensure that your lot numbers comply with the relevant guidelines.
Enabling Lot Tracking at the Item Level
Once you’ve defined your lot numbering scheme, the next step is to enable lot tracking at the individual item level in NetSuite. This is done by editing the item record and checking the “Track Lot Numbers” box on the Inventory subtab.
You can also specify whether lot numbers are required for receiving the item into inventory and whether they must be entered when consuming the item in transactions. These settings ensure that lot information is captured at key points in the item’s lifecycle.
For items that require even more granular tracking, NetSuite also supports serial number tracking. This is ideal for high-value items or products where each unit needs to be uniquely identified for warranty, service, or regulatory purposes. Like lot tracking, serial number tracking is enabled at the item level.
It’s important to note that enabling lot or serial number tracking will impact your inventory processes. Transactions involving lot or serial tracked items will require additional data entry to capture the necessary details. Make sure to account for this in your operational planning and provide adequate training to your team.
Receiving Inventory with Lot Information
With lot tracking enabled, the next phase is to ensure that lot numbers are recorded when receiving inventory into NetSuite. Whether items are purchased from external suppliers or produced in-house, capturing the lot information at the time of receipt is crucial.
On purchase orders, you can specify the lot numbers for each line item being received. NetSuite will automatically create a new lot record if the provided lot number doesn’t already exist. For manufactured goods, the production work order should include the output lot number.
NetSuite also supports the ability to track expiration dates for lots. When receiving inventory, you can enter an expiration date for each lot which will be stored and used for reporting and planning purposes. This is especially valuable for products with limited shelf lives.
To streamline the receiving process, consider integrating barcode scanning. NetSuite supports barcode scanning for inventory transactions, including lot-tracked items. By scanning lot numbers at the time of receipt, you can increase accuracy and efficiency while reducing manual data entry.
Another option to explore is electronic data interchange (EDI) with your suppliers. If your suppliers can provide lot information electronically, you can set up NetSuite to automatically create lot records when inventory is received. This automation can greatly reduce the burden of manual lot data entry.
Lot Tracking in Inventory Movements
As lot-tracked inventory moves through your supply chain, NetSuite keeps a detailed record of each transaction. This includes movements between locations, inventory transfers, customer shipments, and any other type of inventory adjustment.
When transferring lot-tracked items between inventory locations in NetSuite, you’ll be prompted to specify the lot numbers and quantities being moved. This level of detail ensures complete traceability as products flow through your facilities.
Customer shipments and sales orders also require lot information. When fulfilling an order for lot-tracked items, you must specify which lots are being shipped. NetSuite will automatically decrement the available quantity for those lots and maintain a record of which customers received each lot.
This end-to-end traceability is one of the key benefits of lot tracking in NetSuite. At any point, you can see exactly where specific lots are located, which customers they were shipped to, and when they are set to expire. This granular visibility is invaluable for inventory management, quality control, and compliance purposes.
To further enhance your lot tracking capabilities, consider implementing barcoding in your warehouse operations. By scanning lot numbers during picking, packing, and shipping processes, you can ensure accurate data capture and minimize the risk of errors.
Monitoring Lot Expiration Dates
For products with limited shelf lives, closely monitoring lot expiration dates is essential. NetSuite provides tools to help you stay on top of expiring lots and avoid wasted inventory or potential quality issues.
The Lot Expiration Status report in NetSuite shows you a snapshot of all active lots and their expiration dates. You can filter this report to see lots expiring within a certain timeframe, such as the next 30 days. This allows you to proactively plan for the use or disposal of expiring inventory.
NetSuite also offers the ability to set up automated alerts for expiring lots. You can define alert thresholds, such as 60 days before expiration, and specify which users should be notified. These alerts help ensure that key personnel are aware of upcoming expirations and can take appropriate action.
In addition to monitoring expiration dates, it’s important to establish clear processes for handling expired inventory. This may involve physically segregating expired lots, updating their status in NetSuite, and properly disposing of the unusable inventory. Robust expiration date tracking helps minimize the risk of expired products accidentally being used or shipped.
Consider also integrating your lot expiration tracking with demand planning and sales forecasting processes. By factoring in expiration dates, you can optimize your inventory levels and production plans to minimize waste and ensure that you have adequate fresh stock to meet customer demand.
Lot Recall Management
In the event that a product issue is identified and a recall is necessary, having detailed lot tracking information is invaluable. NetSuite’s lot traceability features enable targeted, efficient recalls that minimize disruption and protect your customers.
With end-to-end lot visibility, you can quickly identify which specific lots are affected by a recall. NetSuite’s lot tracking reports show you exactly which customers received the impacted lots, allowing for swift, precise communication and recall management.
Instead of a blanket recall of all products, you can surgically target only the affected lots. This more focused approach reduces waste, minimizes customer inconvenience, and helps protect your brand reputation. Detailed lot records also provide essential documentation for regulators or auditors.
To streamline the recall process, it’s wise to have templates and procedures prepared ahead of time. This could include email templates for customer notifications, step-by-step guides for sales and service teams, and processes for managing recalled inventory. By integrating these into your lot tracking system, you can enable a rapid, coordinated response if a recall is ever necessary.
In addition to reactive recall management, lot tracking data can also be used proactively to identify potential issues before they escalate. By analyzing lot-level quality control data, customer complaints, or return rates, you may be able to spot emerging problems and take corrective action before a full-scale recall is needed.
Lot Tracking for Quality Control
Lot tracking can be a powerful tool for proactive quality control. By monitoring key quality metrics at the lot level, you can identify issues early and prevent larger problems down the line. NetSuite allows you to store quality control data and documents linked to specific lots.
As an example, a food manufacturer could record the results of microbiological tests, allergen analyses, or sensory evaluations for each production lot. If an issue is detected, the impacted lots can be quickly identified and contained before they reach customers.
Over time, lot-level quality data can yield valuable insights. You may uncover trends related to specific suppliers, production lines, or timeframes. This intelligence can drive continuous improvement efforts and help you optimize your supply chain for consistent quality.
To make the most of lot tracking for quality control, consider integrating your quality management processes directly into NetSuite. You can use custom fields on the lot record to capture key quality data points and leverage NetSuite’s workflow engine to automate quality-related tasks and notifications.
For example, you could set up a workflow that automatically creates a quality control task when a new production lot is received, prompting the quality team to perform the necessary tests and inspections. The results can then be recorded directly on the lot record, providing a complete, traceable quality history.
Compliance and Audit Readiness
For businesses in regulated industries, such as pharmaceuticals, medical devices, or food and beverage, robust lot tracking is a must for compliance and audit readiness. Regulations often require detailed traceability records, and the ability to produce these records on demand is critical.
NetSuite’s lot tracking capabilities help ensure that you have the necessary data to meet regulatory requirements. Lot-level details like supplier information, manufacturing dates, test results, and shipping records are securely stored and easily accessible.
In the event of an audit, having organized, complete lot tracking records can greatly streamline the process. Instead of scrambling to piece together information from disparate sources, you can quickly generate reports that provide the required details for specific lots.
It’s also worth considering how your lot tracking data integrates with other compliance-related records in NetSuite, such as quality management processes, safety data sheets, or supplier certifications. By linking this information at the lot level, you can create a comprehensive, cohesive compliance record.
To further enhance your compliance readiness, consider conducting regular mock audits or self-inspections using your lot tracking data. This can help identify any gaps in your records or processes and give you an opportunity to address them before an actual audit occurs.
Integration and Automation
To fully harness the power of lot tracking in NetSuite, it’s important to consider integration and automation opportunities. Lot tracking should not exist in a silo but should be seamlessly integrated with your broader supply chain and inventory management processes.
One key area for integration is barcode scanning. NetSuite supports barcode scanning for inventory transactions, including lot-tracked items. By scanning lot numbers at key points, such as receiving, picking, and shipping, you can increase accuracy and efficiency while reducing manual data entry.
Another opportunity for integration is with your suppliers’ systems. If your suppliers also use NetSuite or can provide lot information electronically, you can explore options for automated data sharing. This could involve automatically creating lot records in your system when you receive inventory from the supplier, streamlining the receiving process.
In terms of automation, NetSuite’s scripting and workflow capabilities offer ample opportunities to streamline lot tracking processes. For example, you could automate the creation of lot-level quality control records based on item receipts, or automatically generate alerts when lots are nearing expiration.
You can also use automation to enforce lot tracking discipline and ensure data integrity. For instance, you could set up validation rules that prevent the completion of certain transactions if the required lot information is missing or invalid.
The goal should be to make lot tracking as seamless and integrated as possible with your day-to-day operations. By leveraging automation and integration, you can realize the benefits of granular traceability without undue manual effort.
Best Practices for Implementing Lot Tracking
To ensure a successful implementation of lot tracking in NetSuite, consider the following best practices:
1. Clearly define your business requirements and goals for lot tracking. What level of granularity do you need? What compliance requirements must be met? Use these requirements to guide your setup and process design.
2. Establish consistent, meaningful lot numbering conventions. Make sure your lot numbers include the necessary information and are easy to interpret at a glance.
3. Train your team on lot tracking processes. Everyone involved in handling lot-tracked inventory should understand the importance of accurate data capture and the specific steps required in NetSuite.
4. Integrate lot tracking with your broader quality management system. Lot-level quality data is most valuable when it’s part of a comprehensive quality program.
5. Regularly review and audit your lot tracking data. Check for completeness, accuracy, and consistency. Address any issues promptly to maintain the integrity of your traceability records.
6. Leverage automation and integration opportunities. Look for ways to streamline lot tracking processes and reduce manual effort through NetSuite’s automation tools and integration capabilities.
7. Stay current with regulatory requirements. Lot tracking requirements can change over time, especially in heavily regulated industries. Regularly review your processes to ensure ongoing compliance.
The Power of Granular Visibility
Implementing advanced lot tracking strategies in NetSuite unlocks a new level of visibility and control over your inventory. From receiving to shipping, you gain a granular view of your products’ journey through the supply chain.
This visibility brings numerous benefits. You can respond quickly and precisely to quality issues, minimizing the impact of recalls. You can provide customers and auditors with detailed traceability information, strengthening trust and compliance. You can uncover opportunities for quality and efficiency improvements that may be hidden at an aggregate level.
Most importantly, robust lot tracking helps ensure that your customers consistently receive high-quality, safe products. In today’s complex, fast-paced supply chain environment, that’s an invaluable advantage.
If you’re looking to take your inventory management to the next level, consider implementing advanced lot tracking strategies in NetSuite. With the right approach and best practices, you can unlock new insights, efficiencies, and competitive advantages.
At EmphOrasoft, we have deep experience helping businesses implement lot tracking and other advanced supply chain capabilities in NetSuite. If you’d like to learn more about how we can support your lot tracking journey, please get in touch. We’d be delighted to discuss your unique requirements and explore how NetSuite can deliver the granular visibility and control your business needs to thrive.
Get in Touch
We know what NetSuite can do and how it can help you. Schedule your free NetSuite assessment today
FAQs:
Lot tracking in NetSuite is a feature that enables businesses to trace specific batches of inventory through their entire lifecycle—from suppliers to end customers. It is essential for industries dealing with perishable goods, regulated products, or items requiring detailed traceability to enhance quality control, streamline compliance, and enable precise recalls.
NetSuite allows you to create customized lot numbering schemes based on your business needs. Consider including information like production dates, product codes, or expiration dates. For example, a food manufacturer might use a format like “20230530-APP-001” to include production date and batch details.
To enable lot tracking for an item, go to the item’s record in NetSuite, navigate to the Inventory subtab, and check the “Track Lot Numbers” box. You can also set rules for when lot numbers must be captured, such as during inventory receipt or consumption.
Tracking expiration dates helps minimize waste and avoid quality issues by proactively managing expiring inventory. NetSuite offers tools like the Lot Expiration Status report and automated alerts to keep you informed about upcoming expirations.
Yes, NetSuite’s lot tracking capabilities allow for precise, targeted recalls. You can identify affected lots, trace them to specific customers, and initiate focused communication and inventory adjustments, minimizing disruption and protecting your brand.
NetSuite provides scripting and workflow tools to automate lot tracking. For example, you can set up workflows to create quality control tasks automatically when a new lot is received or generate alerts for expiring lots. Barcode scanning integration also reduces manual effort.
Industries such as food and beverage, pharmaceuticals, medical devices, and any sector with regulatory or quality requirements benefit significantly from advanced lot tracking. It ensures compliance, supports quality assurance, and enhances operational efficiency.
Lot tracking allows businesses to link quality control data to specific lots. For instance, you can store test results or inspection data directly in NetSuite and use this information to identify trends or address issues proactively.
Yes, NetSuite supports both. While lot tracking is for batches of items, serial number tracking provides unique identification for individual units, which is ideal for high-value products or items requiring warranty or service tracking.
Best practices include: defining clear business requirements, creating consistent lot numbering schemes, training employees, integrating with quality management systems, leveraging automation, and staying updated on regulatory changes. Regular audits ensure the accuracy and reliability of lot data.
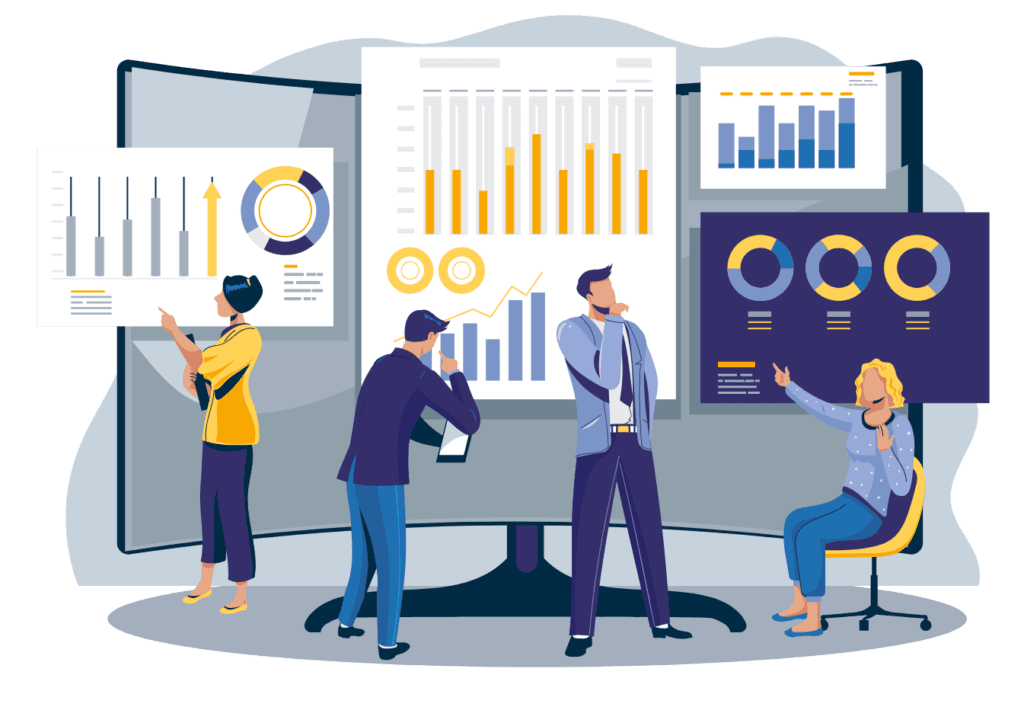