NetSuite’s Quality Management System Implementation Guide
In today’s competitive manufacturing and distribution landscape, delivering high-quality products and services is no longer a differentiator – it’s a basic requirement for staying in business. Customers expect flawless quality, regulators demand strict compliance, and any slip-ups can have devastating consequences for a company’s reputation and bottom line. That’s why more and more organizations are turning to enterprise quality management system (QMS) software to help them streamline their quality processes, automate compliance, and drive continuous improvement.
NetSuite, the world’s leading cloud ERP platform, offers a comprehensive Quality Management System that is fully integrated with its core business management capabilities. Whether you’re a small manufacturer looking to establish formal quality control processes for the first time or a large enterprise aiming to consolidate disparate quality systems into a single platform, NetSuite QMS provides the tools and flexibility you need to manage quality across your entire organization.
In this guide, we’ll take a deep dive into NetSuite’s Quality Management System and show you how to implement it successfully in your business. We’ll cover the key features and benefits of NetSuite QMS, walk through the steps for setting up and configuring the system, and share best practices and tips for driving user adoption and realizing maximum value from your investment. By the end of this guide, you’ll have a clear roadmap for implementing NetSuite QMS and positioning your organization for long-term success.
Why NetSuite for Quality Management?
NetSuite’s cloud-based ERP platform is trusted by over 40,000 organizations worldwide to run their critical business processes, from accounting and inventory management to marketing and customer service. For companies looking to integrate quality management into their core operations, NetSuite QMS offers several key advantages:
1. Seamless integration with NetSuite ERP: NetSuite QMS is built natively on the NetSuite platform, which means it integrates seamlessly with all other NetSuite modules and data. Quality data is automatically tied to specific products, orders, and transactions, giving you a complete, real-time view of quality across your business.
2. Comprehensive quality management capabilities: NetSuite QMS supports end-to-end quality processes, from inspection and non-conformance management to supplier quality and compliance. Its modular architecture allows you to enable specific quality capabilities based on your needs and scale the system as your requirements evolve.
3. Flexible configuration and customization options: NetSuite’s highly configurable platform allows you to tailor the QMS to your unique quality processes and workflows. You can create custom inspection templates, design your own dashboards and reports, and even develop your own quality applications using NetSuite’s SuiteCloud development tools.
4. Real-time quality data and analytics: With NetSuite QMS, quality data is captured at the source and instantly available for reporting and analysis. You can monitor quality metrics in real-time, identify trends and issues early, and make data-driven decisions to drive continuous improvement.
5. Cloud-based accessibility and scalability: As a cloud-based solution, NetSuite QMS can be accessed anytime, anywhere, from any device with an internet connection. It scales easily as your business grows, without the need for costly IT infrastructure or maintenance.
By leveraging NetSuite’s integrated Quality Management System, you can break down data silos, streamline quality workflows, and gain a holistic view of quality performance across your organization. You can improve efficiency, reduce costs, and ultimately deliver higher-quality products and services to your customers.
Planning Your NetSuite QMS Implementation
Before diving into the technical setup of NetSuite’s Quality Management System, it’s important to develop a clear plan and roadmap for your implementation. A well-planned QMS implementation can help you avoid common pitfalls, ensure alignment with business goals, and drive user adoption and success.
Here are the key steps to follow when planning your NetSuite QMS implementation:
1. Define your quality management objectives and KPIs: Start by clearly defining what you hope to achieve with your QMS implementation. Are you looking to reduce defects and rework, improve compliance with regulations, or increase customer satisfaction? Identify the specific quality metrics and KPIs you will use to measure success.
2. Map out your current quality processes and identify areas for improvement: Document your existing quality workflows, from receiving and inspection to production and shipping. Identify any bottlenecks, manual processes, or areas of risk that could be improved with a QMS.
3. Determine the scope of your QMS implementation: Decide which products, processes, and facilities you will include in your initial QMS rollout. You may choose to start with a pilot implementation in a specific area before expanding to other parts of the organization.
4. Identify the key stakeholders and assemble your implementation team: A successful QMS implementation requires collaboration across multiple departments and roles, from quality managers and inspectors to shop floor operators and executives. Identify the key stakeholders who will be involved in or impacted by the QMS and assemble a cross-functional team to lead the implementation.
5. Establish a timeline and milestones for your QMS rollout: Develop a realistic timeline for your QMS implementation, including key milestones such as system configuration, data migration, user training, and go-live. Be sure to build in time for testing and refinement before the full rollout.
6. Develop a training and change management plan: Implementing a QMS involves not just new technology, but also new processes and ways of working. Develop a comprehensive plan for training end-users on the new system and processes, and for managing the organizational change that comes with a QMS implementation.
By investing time upfront to plan your QMS implementation, you can ensure that the system is aligned with your business goals, configured to meet your specific needs, and embraced by users across your organization.
Setting Up Your NetSuite QMS Environment
Once you have a solid implementation plan in place, it’s time to start configuring your NetSuite QMS environment. The setup process involves enabling the Quality Management feature, defining your quality processes and data, and configuring the various QMS modules to support your specific workflows.
Here are the key steps involved in setting up your NetSuite QMS environment:
1. Enable the Quality Management feature: In your NetSuite account, navigate to Setup > Company > Enable Features and enable the Quality Management feature. This will activate the QMS modules and make them available for configuration.
2. Define your quality control processes and workflows: In the Quality Management setup menu, define the high-level processes that make up your quality workflow, such as Inspection, Non-Conformance, Corrective Action, etc. For each process, specify the steps involved, the data to be captured, and the roles and permissions required.
3. Set up quality specifications and inspection plans: Define the quality specifications and criteria for your products and materials, including dimensions, tolerances, and testing requirements. Use these specifications to create inspection plans that specify what needs to be inspected, when, and by whom.
4. Create inspection templates and quality forms: Design the templates and forms that will be used to record quality data, such as inspection sheets, non-conformance reports, and corrective action requests. NetSuite provides a drag-and-drop form builder that allows you to easily create custom forms without coding.
5. Configure alerts and notifications: Set up automated alerts and notifications to keep stakeholders informed of critical quality events, such as failed inspections, overdue corrective actions, or supplier quality issues. NetSuite allows you to define the conditions and recipients for each alert.
6. Establish user roles and permissions: Define the roles and permissions for each user who will access the QMS, such as quality managers, inspectors, and shop floor operators. Specify which modules and data each role can view and edit, and set up approval workflows as needed.
7. Integrate QMS with other NetSuite modules: Configure the integration points between QMS and other NetSuite modules, such as manufacturing, inventory, and purchasing. Ensure that quality data flows seamlessly across the organization and that all relevant transactions and records are linked to quality processes.
8. Test your QMS setup and refine as needed: Before rolling out the QMS to end-users, thoroughly test the system to ensure that it is configured correctly and that all processes and workflows function as intended. Gather feedback from key stakeholders and refine the setup as needed.
By following these steps and leveraging NetSuite’s flexible configuration options, you can set up a QMS environment that is tailored to your organization’s specific quality management needs and processes.
Implementing Quality Control Processes in NetSuite
With your NetSuite QMS environment set up, you can start implementing your core quality control processes in the system. NetSuite provides a range of modules and capabilities to support end-to-end quality management, from inspection and non-conformance handling to supplier quality and compliance.
Here are some of the key quality control processes you can manage in NetSuite QMS:
Inspection Management
NetSuite’s inspection management tools allow you to plan, execute, and document inspections at every stage of the product lifecycle, from incoming raw materials to finished goods. You can:
– Create inspection plans based on product specifications and quality requirements
– Schedule inspections and assign them to specific inspectors or teams
– Record inspection results, including measurements, defects, and pass/fail status
– Generate inspection reports and certificates of analysis
– Track inspection metrics and trends over time
By automating inspection workflows in NetSuite, you can ensure that all products and materials are consistently checked for quality, reduce manual data entry and paperwork, and gain real-time visibility into inspection results.
Non-Conformance and Corrective Action Management
When quality issues or defects are identified, NetSuite’s non-conformance and corrective action (NC/CA) management tools help you track and resolve them efficiently. You can:
– Create non-conformance records that capture details of the issue, affected products, and severity level
– Link non-conformances to specific inspection records, orders, or transactions
– Assign non-conformances to specific teams or individuals for investigation and resolution
– Track the status of non-conformances and corrective actions through to closure
– Conduct root cause analysis and document corrective and preventive actions taken
– Monitor NC/CA metrics and trends to identify areas for improvement
By managing non-conformances and corrective actions in NetSuite, you can ensure that quality issues are addressed promptly and systematically, prevent recurrence of problems, and continuously improve your products and processes.
Supplier Quality Management
NetSuite QMS includes powerful tools for managing the quality of your incoming materials and supplier relationships. You can:
– Track supplier performance and quality metrics, such as defect rates and on-time delivery
– Manage supplier certifications, qualifications, and audit results
– Collaborate with suppliers on quality improvement initiatives and corrective actions
– Integrate supplier quality data with your internal inspection and non-conformance processes
– Generate supplier scorecards and performance reports
By bringing supplier quality management into NetSuite, you can gain end-to-end visibility into your supply chain quality, identify and mitigate supplier risks, and build stronger, more collaborative relationships with your suppliers.
Compliance Management
For companies in regulated industries such as food and beverage, medical devices, and aerospace, NetSuite QMS provides robust tools for managing compliance with quality standards and regulations. You can:
– Map your quality processes to specific standards and regulations, such as ISO 9001, FSSC 22000, or FDA 21 CFR Part 820
– Manage controlled documents, such as SOPs, work instructions, and quality manuals
– Track employee training and certifications related to quality and compliance
– Schedule and conduct internal and external quality audits
– Generate audit-ready documentation and reports for regulators and customers
By automating compliance management in NetSuite, you can streamline your compliance efforts, reduce the risk of non-compliance, and be prepared for audits and inspections at any time.
Driving Continuous Quality Improvement with NetSuite Analytics
One of the most powerful aspects of NetSuite QMS is its ability to capture and analyze quality data across your entire organization. With real-time data and built-in reporting and analytics tools, you can gain deep insights into your quality performance and drive continuous improvement initiatives.
Here are some of the ways you can leverage NetSuite’s analytics capabilities for quality management:
– Monitor quality metrics and KPIs: Track key quality metrics, such as defect rates, inspection pass rates, and supplier performance, in real-time dashboards and reports. Set up alerts to notify you of any deviations from targets.
– Identify trends and patterns: Use NetSuite’s powerful data visualization tools to spot trends and patterns in your quality data, such as recurring defects, seasonal variations, or process bottlenecks. Drill down into specific data points to investigate root causes.
– Benchmark performance across the organization: Compare quality metrics across different products, processes, facilities, or suppliers to identify best practices and areas for improvement. Use benchmarking data to set realistic targets and goals.
– Make data-driven decisions: Use quality data and insights to prioritize improvement initiatives, allocate resources, and measure the impact of changes. NetSuite’s flexible reporting and dashboard tools allow you to slice and dice data in any way you need to support decision-making.
– Share quality insights across the organization: Use NetSuite’s role-based dashboards and reports to share quality performance data with key stakeholders, from executives to shop floor operators. Foster a culture of transparency and continuous improvement by making quality data accessible and actionable.
By leveraging NetSuite’s analytics capabilities, you can transform quality management from a reactive, firefighting mode to a proactive, data-driven approach that drives continuous improvement and business value.
Best Practices for Successful NetSuite QMS Adoption
Implementing a QMS is not just a technology project – it’s a transformative initiative that impacts people, processes, and culture across the organization. To ensure successful adoption of NetSuite QMS and realize the full benefits, consider the following best practices:
1. Secure executive sponsorship and leadership buy-in: Ensure that senior leaders understand the value of quality management and are committed to supporting the QMS implementation. Their visible endorsement and participation can help drive change and overcome resistance.
2. Involve end-users early and often: Engage key stakeholders, such as quality managers, inspectors, and shop floor operators, in the planning and design of the QMS. Solicit their input on requirements, workflows, and user experience to ensure that the system meets their needs and is easy to use.
3. Provide comprehensive training and support: Develop a robust training program that covers not just how to use NetSuite QMS, but also the new quality processes and roles. Provide ongoing support and resources, such as user guides, FAQs, and a helpdesk, to ensure that users can access the information they need to be successful.
4. Start with a pilot and gradually roll out: Begin your QMS implementation with a pilot in a specific area or process, such as incoming inspection or a particular product line. Use the pilot to test the system, gather feedback, and refine the configuration before rolling out to other areas. A phased approach can help manage risk and build momentum.
5. Establish clear ownership and governance: Define clear roles and responsibilities for managing and maintaining the QMS, including system administration, data management, and process ownership. Establish a governance structure and process for making decisions about changes and enhancements to the system.
6. Continuously monitor and measure success: Track key metrics and KPIs to measure the impact of your QMS implementation on quality outcomes, such as defect rates, customer complaints, and cost of quality. Use this data to identify areas for improvement and demonstrate the value of the system to stakeholders.
7. Celebrate successes and share best practices: Recognize and reward individuals and teams who embrace the QMS and drive quality improvements. Share success stories and best practices across the organization to build momentum and encourage adoption.
By following these best practices and taking a holistic, people-centric approach to QMS implementation, you can set your organization up for success with NetSuite QMS and drive long-term quality excellence.
Conclusion
In today’s fast-paced, highly competitive business environment, managing quality effectively is more critical than ever. By implementing a robust, integrated Quality Management System like NetSuite QMS, you can streamline your quality processes, ensure compliance, and drive continuous improvement across your organization.
As you embark on your NetSuite QMS implementation journey, remember that success depends on more than just technology – it requires careful planning, cross-functional collaboration, and a commitment to change management and continuous improvement. By following the steps and best practices outlined in this guide, you can avoid common pitfalls, accelerate time-to-value, and realize the full potential of your QMS investment.
With NetSuite QMS as your foundation, you can build a culture of quality that permeates every aspect of your business, from the shop floor to the top floor. You can create a virtuous cycle of continuous improvement that drives efficiency, reduces costs, and delights customers. Most importantly, you can position your organization for long-term success in an era where quality is not just a competitive advantage, but a fundamental requirement for doing business.
Get in Touch
We know what NetSuite can do and how it can help you. Schedule your free NetSuite assessment today
FAQs:
NetSuite’s QMS is an integrated software module within the NetSuite ERP platform that helps organizations manage their quality processes. It supports tasks like inspection management, non-conformance tracking, supplier quality management, and compliance monitoring, enabling businesses to ensure high-quality standards while streamlining workflows.
NetSuite QMS is natively integrated with the NetSuite ERP platform, providing seamless connectivity with other business operations like inventory, manufacturing, and finance. This integration eliminates data silos, reduces manual data entry, and offers real-time visibility into quality performance across the entire organization.
NetSuite QMS includes features like:
- Inspection management for quality checks at various stages.
- Non-conformance and corrective action tracking.
- Supplier quality management tools.
- Compliance management aligned with regulatory standards.
- Real-time analytics and reporting to drive continuous improvement.
NetSuite QMS provides tools to map quality processes to regulatory standards such as ISO 9001 and FDA 21 CFR Part 820. It offers document control, audit management, employee training tracking, and ready-to-use templates for compliance documentation, ensuring organizations meet regulatory requirements effectively.
Yes, NetSuite QMS is highly configurable. Businesses can create custom inspection templates, define specific workflows, design personalized dashboards, and even develop unique applications using NetSuite’s SuiteCloud tools, ensuring the system aligns with their operational requirements.
Implementing NetSuite QMS involves:
- Defining quality objectives and KPIs.
- Mapping existing quality processes and identifying areas for improvement.
- Configuring the QMS environment, including inspection plans and alerts.
- Integrating QMS with other NetSuite modules.
- Testing the system and training end-users before the full rollout.
NetSuite QMS allows businesses to track supplier performance metrics like defect rates and on-time delivery. It helps manage supplier certifications, facilitates collaboration on quality improvement initiatives, and integrates supplier quality data into internal processes for better decision-making.
NetSuite QMS analytics provide real-time insights into quality metrics, helping businesses monitor performance, identify trends, and address issues proactively. With its robust reporting tools, organizations can benchmark performance, support data-driven decision-making, and foster continuous improvement.
A successful implementation requires a cross-functional team, including quality managers, inspectors, IT professionals, shop floor operators, and executives. Involving key stakeholders from various departments ensures alignment and smooth adoption of the system.
Key best practices include:
- Securing executive sponsorship and buy-in.
- Setting clear quality objectives and KPIs.
- Providing comprehensive training to end-users.
- Regularly monitoring quality data to ensure continuous improvement.
- Maintaining open communication to address user feedback and refine processes.
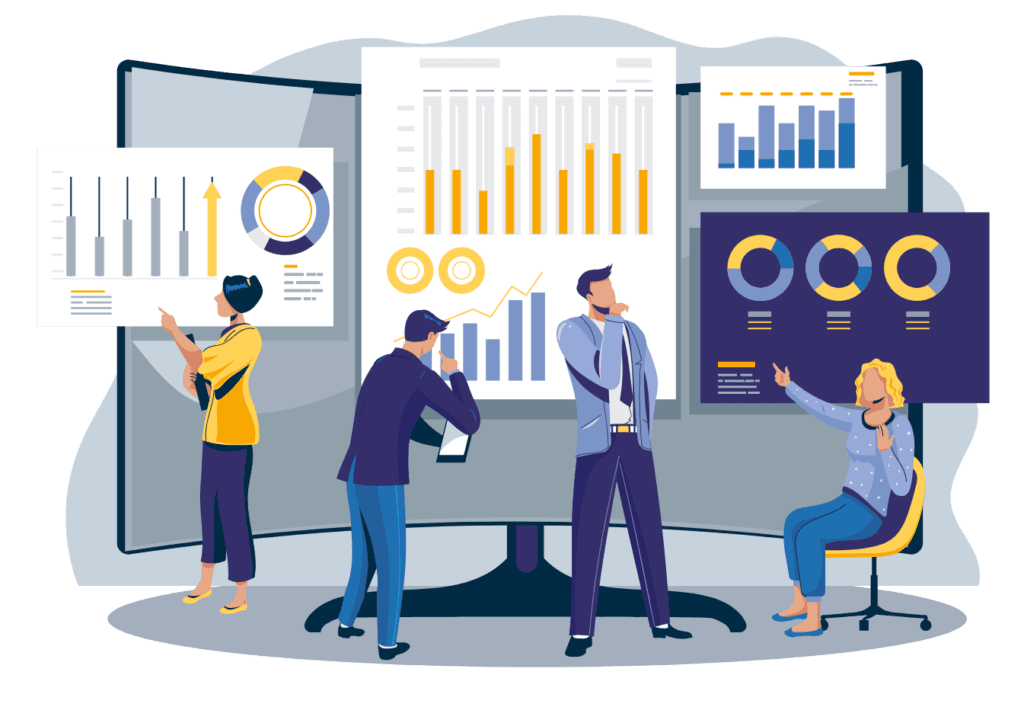