Optimizing Pick, Pack, and Ship Processes in NetSuite
In today’s fast-paced eCommerce landscape, streamlining your pick, pack, and ship processes is essential for meeting customer expectations and driving business growth. NetSuite, a comprehensive cloud-based ERP solution, offers a range of features and tools to optimize your order fulfillment operations. In this blog post, we’ll explore how to leverage NetSuite’s capabilities to enhance efficiency, reduce errors, and improve overall warehouse management.
Understanding the Pick, Pack, and Ship Process in NetSuite
Before diving into optimization strategies, let’s briefly review the pick, pack, and ship process in NetSuite. This process involves several key steps:
1. Order Placement: Customers place orders through various channels, such as your online store, marketplaces, or manual entry by sales reps. NetSuite seamlessly captures these orders, regardless of the source, and centralizes them in a single system.
2. Order Allocation: NetSuite automatically allocates inventory to fulfill the orders based on predefined rules and real-time inventory availability. This ensures that orders are efficiently matched with the appropriate inventory, considering factors such as location, lot numbers, and expiration dates.
3. Pick List Generation: Once orders are allocated, pick lists are generated, guiding warehouse staff to locate and collect the necessary items. NetSuite’s pick list functionality optimizes the picking process by considering factors like item location, quantity, and priority.
4. Picking: Warehouse staff use the pick lists to physically retrieve the items from storage locations. NetSuite supports various picking methods, such as batch picking, wave picking, and zone picking, to maximize efficiency and minimize travel time.
5. Packing: The picked items are then packed into appropriate shipping containers, along with any required packaging materials and documentation. NetSuite’s packing functionality assists in selecting the optimal box size, generating packing slips, and ensuring accurate order fulfillment.
6. Shipping: Packed orders are labeled, manifested, and shipped to customers via selected carriers. NetSuite integrates with major shipping carriers, enabling automated label generation, rate shopping, and real-time tracking information.
By understanding the flow of the pick, pack, and ship process in NetSuite, you can identify areas for improvement and implement targeted optimizations.
Streamlining Picking Operations with NetSuite
Efficient picking is crucial for timely order fulfillment. NetSuite offers several features to streamline your picking processes:
1. Mobile Picking: Utilize NetSuite’s mobile app to enable warehouse staff to pick orders directly from their mobile devices. This eliminates the need for paper pick lists and reduces picking errors. The mobile app provides real-time access to pick lists, item locations, and inventory information, empowering pickers to work efficiently and accurately.
2. Wave Picking: Implement wave picking to consolidate multiple orders into a single pick list. This approach minimizes travel time and improves picking efficiency. NetSuite allows you to define wave criteria based on factors like order priority, shipping method, or customer segment, ensuring that orders are picked in the most optimal sequence.
3. Zone Picking: Divide your warehouse into zones and assign pickers to specific areas. Zone picking reduces walking distance and enhances picker productivity. NetSuite supports the configuration of zones based on product categories, velocity, or storage requirements, enabling pickers to focus on their assigned areas and minimize cross-zone movement.
4. Pick Path Optimization: Configure NetSuite to generate pick lists based on optimized pick paths. This ensures that pickers follow the most efficient route through the warehouse, minimizing travel time. NetSuite’s pick path optimization takes into account factors like item location, proximity, and picking sequence to determine the optimal path for each pick list.
By leveraging these NetSuite features, you can significantly improve picking speed, accuracy, and overall warehouse efficiency. Pickers can work more efficiently, reducing the time required to fulfill orders and increasing customer satisfaction.
Enhancing Packing Efficiency in NetSuite
Optimizing your packing processes is essential for ensuring orders are securely packaged and ready for shipping. Consider these strategies:
1. Packing Stations: Set up dedicated packing stations equipped with all necessary materials, such as boxes, tape, and labels. This reduces the time spent searching for supplies and improves packing efficiency. NetSuite’s packing functionality integrates seamlessly with packing stations, providing packers with real-time access to order details, packing instructions, and packaging requirements.
2. Packing Slips: Configure NetSuite to automatically generate packing slips with each order. This eliminates manual data entry and ensures accurate documentation. Packing slips can include important information like order details, customer information, and special instructions, streamlining the packing process and reducing errors.
3. Cartonization: Utilize NetSuite’s cartonization feature to automatically determine the optimal box size for each order. This minimizes packaging waste and shipping costs. NetSuite’s cartonization algorithm considers factors like item dimensions, weight, and fragility to recommend the most suitable packaging options, ensuring orders are safely and efficiently packed.
4. Packing Automation: Integrate NetSuite with automated packing systems, such as box erectors or void fill dispensers. Automation speeds up the packing process and reduces labor requirements. NetSuite can seamlessly communicate with these systems, triggering automated actions based on order specifications and packing requirements.
By implementing these packing optimizations, you can streamline your packing operations, reduce errors, and improve overall fulfillment efficiency. Packers can work more productively, ensuring orders are accurately and securely packaged for shipping.
Automating Shipping with NetSuite
NetSuite provides robust shipping functionality to automate and optimize your shipping processes:
1. Carrier Integration: Integrate NetSuite with your preferred shipping carriers to automatically generate shipping labels, track packages, and calculate shipping costs. NetSuite supports integration with major carriers like FedEx, UPS, and USPS, enabling seamless communication and data exchange. This eliminates manual data entry and reduces the risk of shipping errors.
2. Rate Shopping: Use NetSuite’s rate shopping feature to compare shipping rates from multiple carriers and select the most cost-effective option for each order. NetSuite can automatically retrieve real-time shipping rates based on factors like package dimensions, weight, and destination, helping you optimize shipping costs and choose the best carrier for each shipment.
3. Shipping Rules: Set up shipping rules in NetSuite to automatically assign the appropriate shipping method based on order weight, destination, or customer preferences. Shipping rules ensure that orders are shipped using the most suitable method, considering factors like delivery time, cost, and customer requirements. This automation reduces manual decision-making and improves shipping accuracy.
4. Batch Shipping: Process multiple orders simultaneously using NetSuite’s batch shipping functionality. This saves time and streamlines the shipping process. Batch shipping allows you to consolidate orders going to the same destination or carrier, generating shipping labels and documentation in bulk. This feature significantly reduces the effort required to process large volumes of shipments.
5. Shipping Notifications: Configure NetSuite to automatically send shipping notifications and tracking information to customers, reducing inquiries and improving customer satisfaction. Shipping notifications keep customers informed about the status of their orders, providing them with real-time updates on shipment progress. This proactive communication enhances the customer experience and builds trust in your brand.
By leveraging NetSuite’s shipping automation capabilities, you can reduce manual effort, minimize shipping errors, and optimize shipping costs. Automated shipping processes enable faster order processing, improve accuracy, and enhance overall operational efficiency.
Real-Time Inventory Tracking with NetSuite
Accurate inventory tracking is critical for efficient order fulfillment. NetSuite provides real-time visibility into your inventory levels:
1. Bin Management: Implement NetSuite’s bin management feature to track inventory at a granular level. This enables precise picking and reduces the risk of stock-outs. Bin management allows you to define specific storage locations within your warehouse, such as racks, shelves, or bins, and assign inventory to these locations. This level of inventory tracking ensures accurate picking and facilitates efficient replenishment.
2. Cycle Counting: Perform regular cycle counts using NetSuite’s inventory management tools. This helps maintain inventory accuracy and identifies discrepancies. Cycle counting involves periodically counting a subset of your inventory and comparing it against the recorded quantities in NetSuite. This proactive approach helps catch and rectify any inventory discrepancies before they impact order fulfillment.
3. Low Stock Alerts: Set up low stock alerts in NetSuite to receive notifications when inventory levels fall below predefined thresholds. This enables proactive replenishment. Low stock alerts ensure that you are aware of potential stock-outs well in advance, allowing you to take timely action to reorder or transfer inventory from other locations. This helps maintain optimal inventory levels and prevents delays in order fulfillment.
4. Inventory Allocation: Utilize NetSuite’s inventory allocation capabilities to reserve inventory for specific orders or channels. This prevents overselling and ensures accurate availability. Inventory allocation allows you to set aside inventory for high-priority orders, specific customers, or sales channels, ensuring that the required stock is available when needed. This feature helps manage inventory effectively and reduces the risk of overselling or stockouts.
By harnessing NetSuite’s real-time inventory tracking features, you can optimize inventory management, reduce stockouts, and improve order fulfillment accuracy. Real-time visibility into inventory levels enables proactive decision-making, efficient replenishment, and accurate order promising.
Integrating NetSuite with Warehouse Automation Systems
To further optimize your pick, pack, and ship processes, consider integrating NetSuite with warehouse automation systems:
1. Conveyor Systems: Integrate NetSuite with conveyor systems to automate the movement of products through your warehouse. This reduces manual handling and speeds up order processing. Conveyor systems can be seamlessly integrated with NetSuite, enabling automated routing of picked items to packing stations or shipping zones. This integration streamlines the flow of goods and minimizes manual intervention.
2. Pick-to-Light Systems: Implement pick-to-light systems that integrate with NetSuite to guide pickers to the correct locations. This improves picking accuracy and efficiency. Pick-to-light systems use light indicators to direct pickers to the exact location and quantity of items to be picked. NetSuite can communicate with these systems, triggering the lights based on the pick lists and updating inventory levels in real-time.
3. Automated Storage and Retrieval Systems (ASRS): Integrate NetSuite with ASRS to automate the storage and retrieval of inventory. This maximizes storage density and reduces picking times. ASRS systems use robotic technology to store and retrieve items from high-density storage locations. NetSuite can interface with ASRS systems, directing the retrieval of items based on order requirements and updating inventory records accordingly.
4. Robotics: Leverage robotic systems that integrate with NetSuite to automate picking, packing, and sorting tasks. Robotics can significantly enhance warehouse productivity. NetSuite can communicate with robotic systems, providing them with order details, item locations, and packing instructions. Robotic systems can then perform tasks like picking, sorting, and packaging, reducing manual labor and increasing efficiency.
By integrating NetSuite with warehouse automation systems, you can take your pick, pack, and ship processes to the next level, achieving even greater efficiency and scalability. Automation integration enables seamless communication between NetSuite and your warehouse systems, optimizing workflows and driving operational excellence.
Implementing Best Practices for NetSuite Pick, Pack, and Ship
In addition to leveraging NetSuite’s features and integrations, consider implementing these best practices to optimize your pick, pack, and ship processes:
1. Warehouse Layout Optimization: Design your warehouse layout to minimize travel distances and maximize efficiency. Consider factors such as product velocity, storage requirements, and workflow. Optimize the placement of fast-moving items closer to packing stations, and organize your warehouse into logical zones based on product categories or picking frequency. A well-designed layout reduces picking time and improves overall efficiency.
2. Standard Operating Procedures (SOPs): Develop and document SOPs for each stage of the pick, pack, and ship process. Clear SOPs ensure consistency and reduce errors. Create detailed procedures for picking, packing, and shipping, including guidelines for handling special items, packaging requirements, and quality control checks. Regularly train your staff on these SOPs to maintain high standards and minimize deviations.
3. Training and Cross-Training: Provide thorough training to your warehouse staff on NetSuite’s functionalities and your specific processes. Cross-train employees to handle multiple tasks, increasing flexibility and resilience. Ensure that your team is well-versed in using NetSuite’s features, such as mobile picking, wave picking, and shipping automation. Cross-training allows staff to adapt to fluctuations in order volume and cover for absences, maintaining operational continuity.
4. Performance Metrics: Establish key performance indicators (KPIs) to measure the efficiency of your pick, pack, and ship processes. Monitor metrics such as order accuracy, cycle time, and productivity to identify areas for improvement. Use NetSuite’s reporting and analytics capabilities to track these metrics in real-time, enabling data-driven decision-making. Regularly review performance data to identify bottlenecks, optimize processes, and set benchmarks for continuous improvement.
5. Continuous Improvement: Foster a culture of continuous improvement within your warehouse operations. Encourage feedback from staff, conduct regular process reviews, and implement ongoing optimizations. Engage your team in identifying areas for improvement, gathering suggestions, and implementing changes. Continuously monitor the impact of optimizations and make data-driven adjustments to refine your processes further. Embrace a mindset of ongoing learning and adaptation to stay ahead of industry best practices.
By adopting these best practices alongside NetSuite’s capabilities, you can create a highly efficient and effective pick, pack, and ship operation. Implementing these practices ensures that your warehouse processes are optimized, your team is well-trained and empowered, and your operations are continuously improving to meet the evolving demands of your business.
Conclusion
Optimizing your pick, pack, and ship processes in NetSuite is crucial for streamlining order fulfillment, reducing errors, and enhancing customer satisfaction. By leveraging NetSuite’s features such as mobile picking, wave picking, cartonization, and shipping automation, you can significantly improve warehouse efficiency. Integrating NetSuite with warehouse automation systems and implementing best practices further elevates your pick, pack, and ship operations.
At Emphorasoft, our team of NetSuite experts can help you optimize your warehouse processes and unlock the full potential of NetSuite’s capabilities. We have a deep understanding of NetSuite’s functionality and extensive experience in implementing best practices for pick, pack, and ship operations. Our consultants can work closely with your team to assess your current processes, identify areas for improvement, and develop a tailored optimization plan.
Whether you need assistance with NetSuite configuration, integration with warehouse automation systems, or training your staff on best practices, Emphorasoft is here to support you every step of the way. We are committed to helping businesses like yours achieve operational excellence and drive growth through efficient and effective warehouse management.
Contact us today to learn more about how we can assist you in streamlining your pick, pack, and ship operations in NetSuite. Our team is ready to provide you with the expertise and guidance you need to take your order fulfillment processes to the next level. Let us help you unlock the full potential of NetSuite and achieve a competitive edge in the eCommerce landscape.
Get in Touch
We know what NetSuite can do and how it can help you. Schedule your free NetSuite assessment today
FAQs:
The pick, pack, and ship process in NetSuite involves capturing customer orders, allocating inventory, generating pick lists, retrieving items from storage (picking), securely packaging them (packing), and shipping them to customers. NetSuite provides tools to streamline and automate each step, ensuring efficiency and accuracy.
NetSuite enhances picking efficiency through features like mobile picking (real-time access via mobile devices), wave picking (consolidating multiple orders into a single pick list), zone picking (dividing warehouses into zones), and pick path optimization (minimizing travel time with optimized routes).
Yes, NetSuite offers several features to automate and streamline packing, including cartonization (determining the best box size automatically), packing slips (auto-generated documentation), and integrations with packing automation tools like box erectors and void fill dispensers.
NetSuite integrates with major shipping carriers like FedEx, UPS, and USPS. It automates label generation, calculates real-time shipping costs, enables rate shopping to choose cost-effective options, and provides real-time tracking for better visibility and customer satisfaction.
Wave picking is a method of grouping multiple orders into a single pick list based on criteria such as order priority, shipping method, or product type. NetSuite’s wave picking functionality helps minimize travel time and streamline operations by optimizing how orders are picked.
NetSuite provides real-time inventory visibility through features like bin management (tracking inventory at specific locations), cycle counting (ensuring inventory accuracy), and low stock alerts (proactive replenishment). These features reduce stockouts and improve order accuracy.
Yes, NetSuite integrates with systems like conveyor systems, pick-to-light technology, automated storage and retrieval systems (ASRS), and robotics. These integrations enhance operational efficiency by automating tasks like picking, sorting, and moving products.
Cartonization in NetSuite is the process of automatically determining the best box size for an order based on item dimensions, weight, and fragility. It minimizes packaging waste, reduces shipping costs, and ensures items are securely packed for transport.
NetSuite’s batch shipping feature allows users to process multiple orders at once. This functionality is particularly useful for consolidating shipments to the same destination or carrier, significantly reducing the time required for manual shipping tasks.
Best practices include designing an efficient warehouse layout, implementing standard operating procedures (SOPs), training staff on NetSuite tools, using KPIs to monitor performance, and fostering a culture of continuous improvement. These strategies, combined with NetSuite’s robust features, enhance efficiency and reduce errors.
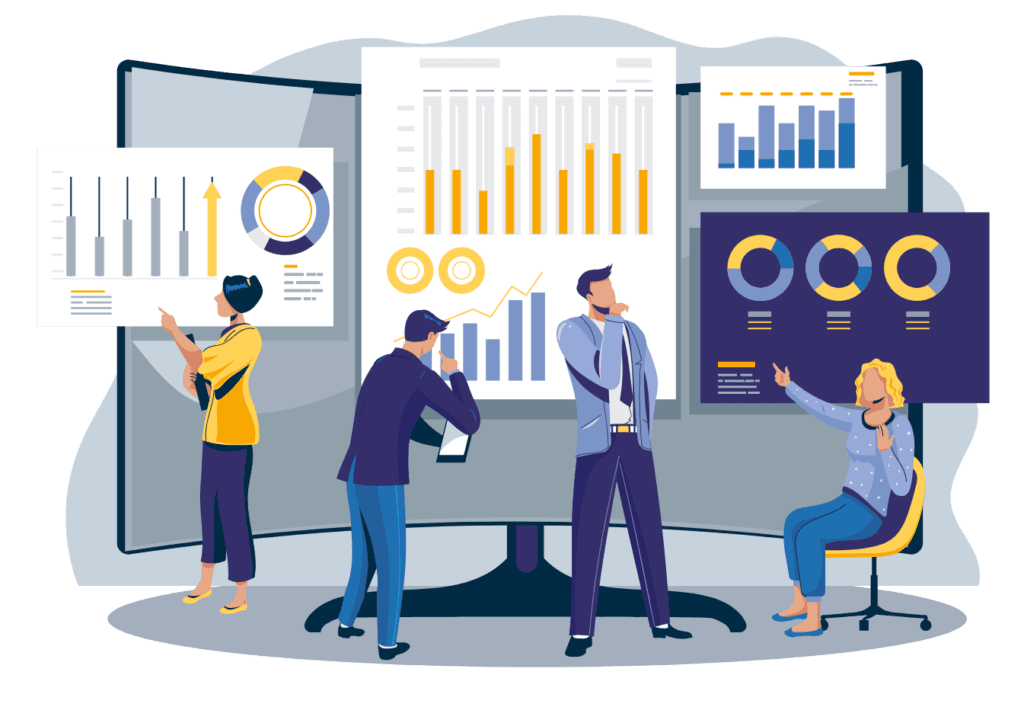